Detrimental Effects of Sub-Par Water
Scale or salt buildup occurs in systems that are high in magnesium or calcium carbonates, which are common in tap water. Scale is likely to form on hot metal surfaces in the cooling system, and in areas that have slow or fast flow. When scale forms on the metal, it creates “hot spots” where the heat cannot pass through the metal as efficiently. Only 1/16th of an inch of scale can reduce the cooling system heat transfer efficiency by 40%! This can result in overheating of the engine and corrosion at the hot spots.
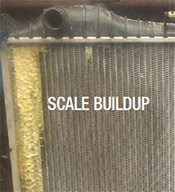
In addition to scale buildup, high mineral content in water can cause inhibitor “drop-out.” High mineral content can change the solubility of inhibitors in the solution and cause some of the inhibitors to come out of solution or “drop out.” This can result in a white precipitate which can clog the radiator and reduce heat transfer. Also, the inhibitors will no longer be in solution at the levels designed to prevent corrosion!

Questions around color are the most common questions that our technical group receives. While color can be an indicator of technology, there are many exceptions. The American Trucking Association’s Technology and Maintenance Council (TMC) makes the following recommendations around color:
Red – Organic Acid Technology
Purple/Pink – Fully Formulated Conventional
Green – Conventional Low Silicate
While these are proper guidelines, they oversimplify the color situation within the industry. Since there are no criteria that manufacturers and OEMs must follow, colors abound. For instance, if you know that your antifreeze is yellow and try to top off based on color, you could be topping off with any of the four technologies that can typically be yellow! Instead of thinking about color, start with the technology best suited for the application.
When in doubt regarding coolant chemistry, use OEM specifications and/or KOST USA to help determine your coolant’s chemistry. Many OEM coolant specifications require a specific chemistry, like heavy duty organic acid technology, and the KOST USA sales team can help determine appropriate fluid.
High sulfate and chloride levels can lead to excessive corrosion. For example, ASTM suggests limiting sulfate to 100ppm max. KOST USA performed corrosion testing on a competitive coolant we found that contained ~4600ppm sulfate and the results were dramatic – the steel sample corroded extensively! Don’t let this be the inside of your cooling system.
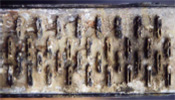
Water Specifications
Now that we know why we should use high-quality water, let’s talk about what defines high quality. An excellent place to start is ASTM D3306, arguably the definitive specification for light- duty antifreeze/coolant. To meet ASTM D3306, a manufacturer must use water that complies with the following specifications when blending ready-to-use or prediluted antifreeze/coolant:
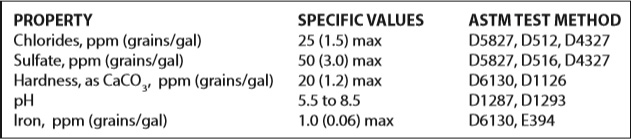
KOST USA complies to these stringent requirements for all water used in the production of antifreeze/coolant. When you buy Ready-To-Use or Prediluted antifreeze/coolant, you are ensuring that the water is top quality.
Performing your own dilutions can be a cost-saving choice if your water source is compliant with ASTM recommendations. Antifreeze/Coolant produced at KOST USA contains anti-scale chemicals to help protect your cooling system against moderately hard water, as most municipal water facilities do not hold water to the same standards suggested by ASTM. Use a field test kit (available through KOST USA sales representative), over the counter test strips, or send a sample to KOSTCare, KOST USA’s program for analysis and recommendations.
Have a look at the chart below to see how many color variations are typically found within different technologies.
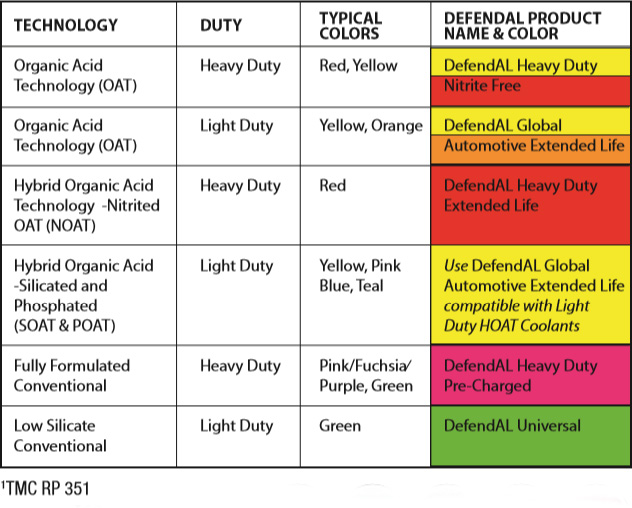