Home » Stationary Engine Coolants
Home » Stationary Engine Coolants
STATIONARY ENGINE COOLANT

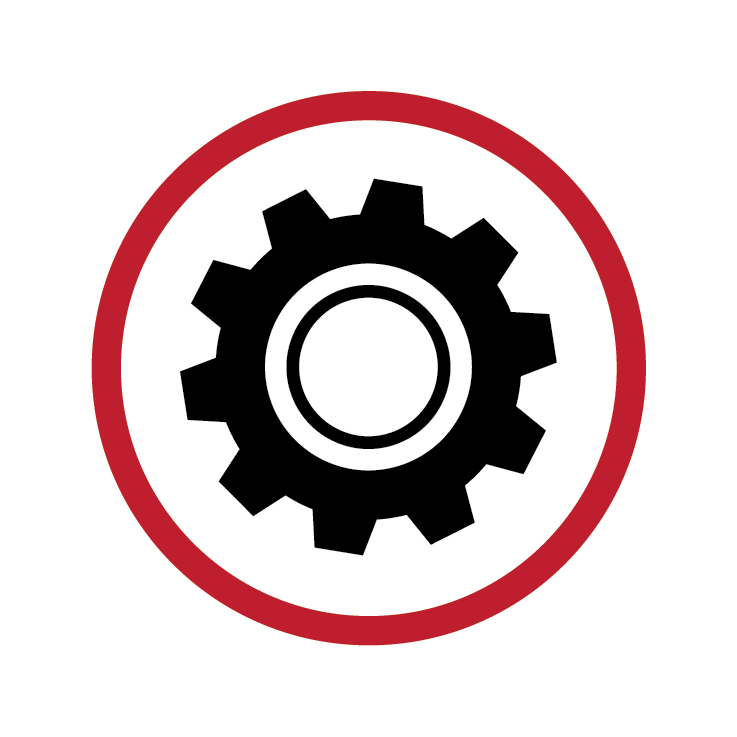
KOST USA Stationary Engine Coolants are superior inhibited glycols designed for the demanding requirements of stationary engines. They are fortified with various corrosion inhibitors to prevent corrosion of many different system components and metals. These inhibitors protect wet sleeve liners from premature cavitation and corrosion. They also are composed of anti-scaling, de-foamers and anti-fouling compounds that enhance fluid durability and equipment life. The operating temperatures are between -60°F (-51°C) and 275°F (135°C).
All Stationary Engine Coolants produced by KOST USA are available at various dilutions with deionized water. If it is decided to buy a concentrate from KOST USA, it is strongly recommended that the water used be of deionized, distilled or reverse osmosis. Our product is engineered with inhibitors and additives that assist in minimizing contamination from municipal and well water. However, excess water hardness and elevated levels of chlorides, sulfates, and fluorides found in most municipal and well water can shorten the fluid life as they continue to build after each addition.
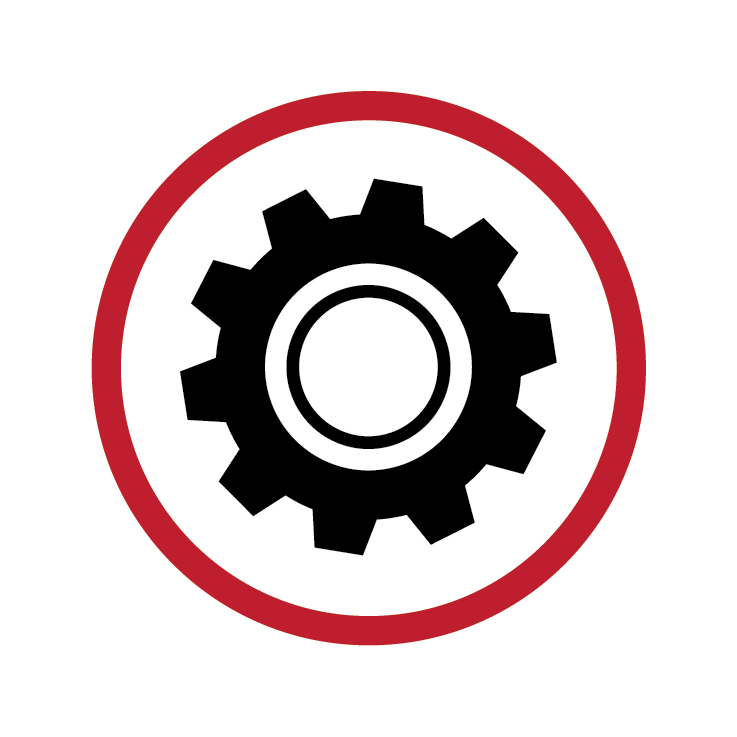
STATIONARY ENGINE COOLANT

KOST USA Stationary Engine Coolants are superior inhibited glycols designed for the demanding requirements of stationary engines. They are fortified with various corrosion inhibitors to prevent corrosion of many different system components and metals. These inhibitors protect wet sleeve liners from premature cavitation and corrosion. They also are composed of anti-scaling, de-foamers and anti-fouling compounds that enhance fluid durability and equipment life. The operating temperatures are between -60°F (-51°C) and 275°F (135°C).
All Stationary Engine Coolants produced by KOST USA are available at various dilutions with deionized water. If it is decided to buy a concentrate from KOST USA, it is strongly recommended that the water used be of deionized, distilled or reverse osmosis. Our product is engineered with inhibitors and additives that assist in minimizing contamination from municipal and well water. However, excess water hardness and elevated levels of chlorides, sulfates, and fluorides found in most municipal and well water can shorten the fluid life as they continue to build after each addition.
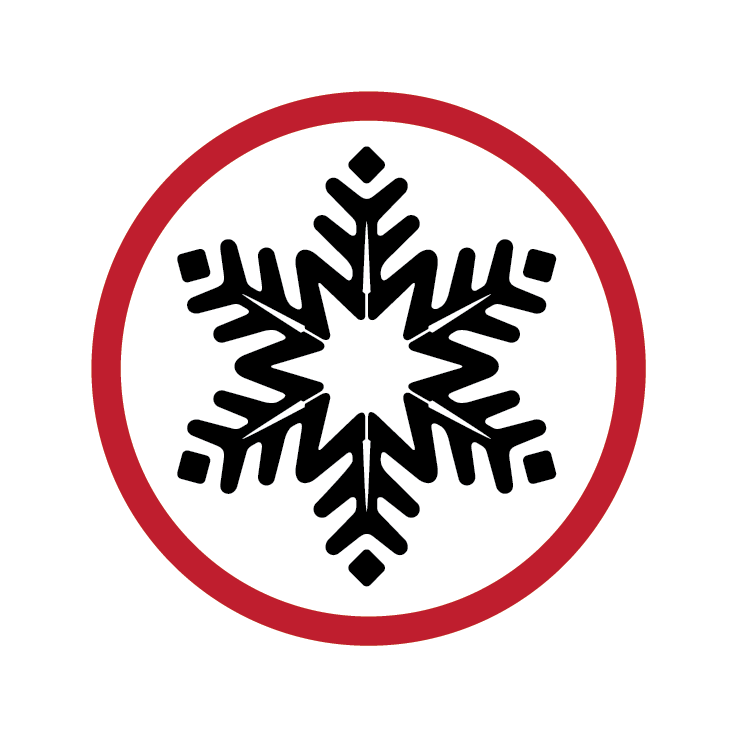
STATIONARY ENGINE COOLANT

KOST USA Stationary Engine Coolants are superior inhibited glycols designed for the demanding requirements of stationary engines. They are fortified with various corrosion inhibitors to prevent corrosion of many different system components and metals. These inhibitors protect wet sleeve liners from premature cavitation and corrosion. They also are composed of anti-scaling, de-foamers and anti-fouling compounds that enhance fluid durability and equipment life. The operating temperatures are between -60°F (-51°C) and 275°F (135°C).
All Stationary Engine Coolants produced by KOST USA are available at various dilutions with deionized water. If it is decided to buy a concentrate from KOST USA, it is strongly recommended that the water used be of deionized, distilled or reverse osmosis. Our product is engineered with inhibitors and additives that assist in minimizing contamination from municipal and well water. However, excess water hardness and elevated levels of chlorides, sulfates, and fluorides found in most municipal and well water can shorten the fluid life as they continue to build after each addition.