Benefits of Heavy Duty Nitrite Free Coolants
Heavy-duty engine technology has come a long way in the past20 years, and coolant technology has had to keep up to protect modern HD engines. However, some operators are still using outdated technology. You didn’t stick with dial-up internet instead of switching to high-speed: so, stop buying out of date technology for your heavy-duty equipment! There are numerous benefits to switching to a heavy-duty nitrite-free (HDNF) OAT coolant like DefendAL HD NF ELC – let’s examine them in more detail.
Modern HD Engines Need More Advanced Technology
Modern HD engines are different than pre-2000 HD engines. Increased aluminum usage means that the inhibitors that we are using the protect the cooling system should change: organic acid inhibitors protect aluminum better than the borated and phosphated inhibitors in conventional technology coolant. In addition, HD engines have been designed to produce fewer emissions by introducing measures such as exhaust gas recirculation (EGR) and diesel particulate filters. These innovations put additional stress on the coolant. The EGR system alone adds an extra 25-30% more heat rejection to the coolant! Modern diesel engines need a more robust coolant to withstand the additional heat: since nitrite breaks down in higher-heat applications, nitrite-free coolant is designed to meet these needs though the use of molybdate, a more temperature-stable inhibitor.
Better Technology Comes with Numerous Benefits
Now that you know the technical reason for using nitrite-free coolant, let’s talk about the range of other benefits that this technology offers.
1. Reduced Maintenance
Avoid costly mistakes such as the over-addition of SCA or poor maintenance practices: HD NF coolant can typically be maintained through top-off alone! Say goodbye to lab samples, test strips, and the addition of SCA – simply top-off and go. Just check the coolant’s appearance/pH every 300,000 miles and top off as needed with DefendAL HD NF ELC 50/50.
2. Cost Savings
While HD NF coolant is more expensive initially, the reduced maintenance leads to significant cost savings over the coolant’s life. Compared to a conventional technology heavy-duty coolant, nitrite-free coolant saves approximately 70%!
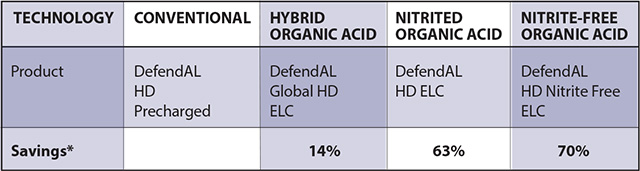
3. Use Across the Fleet
Most fleets have multiple coolants on their shelves to service various types of vehicles and engines. However, HD nitrite-free coolant can, in many cases, satisfy all coolant needs with just one coolant technology.
The lack of nitrites in this heavy-duty coolant means that it is not harsh on primarily aluminum automotive cooling systems. In addition, most HD OEMs have approved this technology for use in their equipment: use it in Detroit Diesel, Cummins, CAT, MAN, John Deere, Komatsu, Mack, Navistar, and others. Finally, HD NF coolant technology is backward – compatible: safe for old and new equipment. That makes HD NF coolant the most versatile coolant that can be bought!
Importance of Glycol Concentration
A common question regarding heat transfer fluids is: “Can I use a 20% glycol fluid in my heat transfer system”? The short answer is: “Yes” if you want to incur decreased system performance year after year, expensive maintenance overhauls, and extended downtime due to equipment failure. Or, the long answer: NO.
The properties of a heat transfer fluid are strongly correlated to the amount of glycol in the system, including corrosion protection and biofouling. Let’s review both:
Corrosion Protection:
Heat transfer fluids (HTF) typically contain inhibitors as a ratio to the percent glycol. With HTFs, each “cut” is from concentrate. Therefore, increasing the water content decreases the inhibitor content. ASTM D8039 sets the specification for ASTM D8040, which test fluids at a 30% glycol to ensure products can adequately protect systems against corrosion. All KOSTChill fluids meet or exceed ASTM D8039 corrosion protection requirements. Fluids below 30% glycol do not meet ASTM D8039 and may not provide adequate corrosion protection.
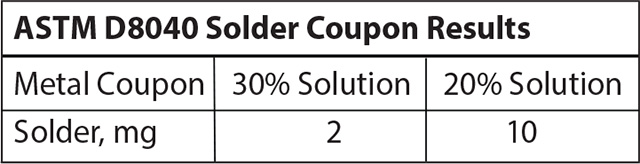
An example of this is demonstrated between a 30% fluid that meets ASTM D8039 specification, and the same fluid decreased to 20%. Data shows that with decreased inhibitors, lead solder becomes highly susceptible to corrosion ranging from 2 milligrams of corrosion to 10 mg of corrosion. ASTM D8040 is the corrosion test method used in the heat transfer fluid specification to measure corrosion; higher values equals higher corrosion rates and metal loss.
Biofouling:
Biofouling results from microbial growth in a heat transfer system that leads to decreased thermal transfer, fluid degradation, and clogged filters.
Biofouling is the result of microbes forming biofilms, which are layers of microbes and extracellular protective material that attach to the heat transfer system’s walls. The impact is that biofilms create resistance to fluid flow and reduces heat transfer efficiency; once created, they are difficult to eradicate (meaning biofouling is more likely to reoccur).
Not only do microbes form performance reducing biofilms, under the right the conditions the glycol and inhibitors become an excellent food source. Microbes will consume or “eat” the glycol and inhibitors in the fluid and produce metabolic by-products that reduce pH and accelerates further fluid degradation and deceases corrosion protection.
Lastly, microbial growth can lead to HTF filters becoming clogged quickly, which leads to unnecessary system downtime and maintenance to resolve the issue and get the system up and running. leads to unnecessary system downtime to perform maintenance to resolve the issue and get the system up and running. KOST has helped diagnose systems that have suffered severe performance losses or have clogged due to biofouling. The one common contributing factor is that the percentage of glycol in the fluid for these systems were below the recommended minimum of a 30% glycol concentration.
Glycol concentration greater than 25% creates an environment inhospitable to microbes by limiting their ability to reproduce and helps maintain fluid pH above their preferred growth range. To ensure that HTF’s meet ASTM D8039 specification for corrosion protection and maintaining an environment inhospitable to microbes, KOST recommends using Heat Transfer Fluids with at least 30% or greater glycol content.